Why Does Copper Need a Surface Finish? Copper is a popular material in electronics, plumbing, and various industrial applications due to its excellent electrical conductivity, thermal performance, and malleability. However, while copper offers many benefits, it also has one notable drawback: it is highly prone to oxidation and tarnishing when exposed to air and moisture. This is why applying a surface finish to copper is essential for preserving its performance and extending its lifespan. But why exactly does copper need a surface finish, and what benefits does it bring? The nature of copper oxidation When copper is exposed to air, it reacts with oxygen, leading to the formation of copper oxide on its surface. Over time, this oxide layer can develop into a green patina, which you often see on old copper roofs or statues. While this patina can be visually appealing in architecture, it is far from ideal in industrial applications, especially in electronics, where a clean, conductive surface is critical. Impact of oxidation on performance Oxidation increases the electrical resistance of copper surfaces, which can negatively impact the performance of electronic components and connections. In high-frequency applications, even a thin oxide layer can lead to signal loss and unreliable connections. In plumbing, oxidation can lead to contamination of water and reduced flow efficiency. Why a surface finish is essential A surface finish acts as a protective barrier, preventing copper from direct contact with air and moisture, thereby slowing down or completely stopping the oxidation process. Here are the key benefits of applying a surface finish on copper:
Common surface finishes for copper Several types of surface finishes can be applied to copper, depending on its application: Tin plating: Widely used for electronics, tin plating offers excellent solderability and corrosion resistance. Choosing the right finish The choice of surface finish depends on the intended application of the copper component. For instance, in printed circuit boards (PCBs), a finish like ENIG (Electroless Nickel Immersion Gold) or OSP (Organic Solderability Preservative) is often chosen to maintain solderability and conductivity over time. For plumbing, tin or nickel plating may be used to prevent water contamination and corrosion. Conclusion: protect your copper for lasting performance While copper is a highly versatile and conductive material, its tendency to oxidize can lead to performance issues and a reduced lifespan if left unprotected. Applying a surface finish is not just an option but a necessity for industries that rely on copper’s unique properties. It ensures corrosion resistance, maintains conductivity, and supports the quality of the final product. If you work with copper in your production process, consider which surface finish aligns best with your application to protect your investment and guarantee reliable performance. |
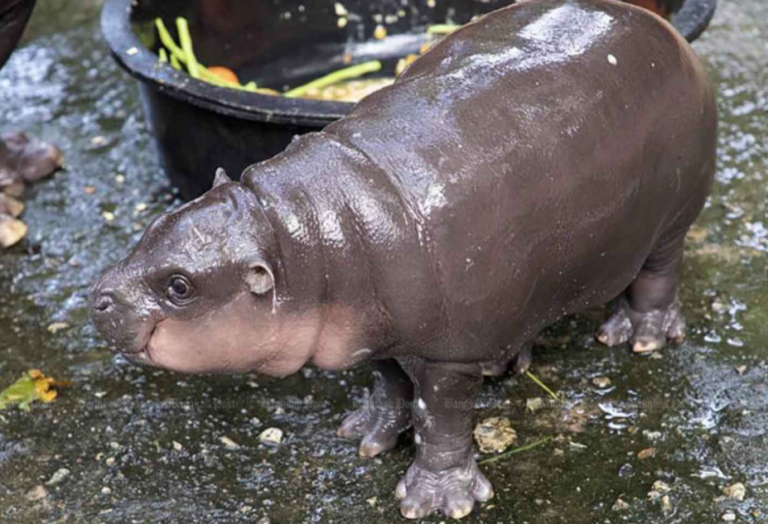
Moo Deng the Hippo: A Symbol of Conservation and Mystery
When it comes to wildlife conservation, every individual animal tells a story that sparks interest